探索一种高温压力传感器封装结构的奥秘
你有没有想过,那些在极端环境下默默工作的传感器,它们是如何在烈火与高压中保持精准测量的?今天,就让我们一起深入探索一种特殊的高温压力传感器封装结构,看看它是如何突破技术极限,为工业领域带来革命性变化的。
高温压力传感器的挑战
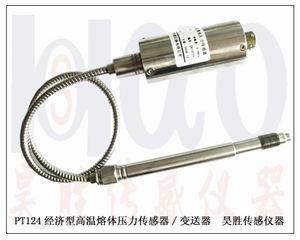
想象在超过500摄氏度的熔炉中,或者是在几千个标准大气压的水下,仍然需要精确测量压力变化,这谈何容易。传统的传感器在这里早就已经不堪重负,要么被高温熔化,要么被高压压垮。工业领域对能够在极端环境下稳定工作的压力传感器的需求日益迫切,这促使工程师们不断寻找新的解决方案。
在这样的背景下,一种创新的高温压力传感器封装结构应运而生。它不仅仅是对现有技术的简单改进,而是一次对材料科学、封装工艺和设计理念的全面革新。这种封装结构必须具备超高的耐温性能、优异的抗压能力,同时还要保证传感器的长期稳定性和可靠性。
核心材料的选择
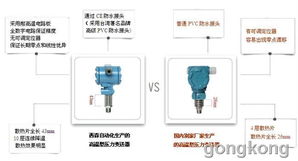
任何一款高性能传感器的诞生,都离不开核心材料的选择。对于高温压力传感器而言,材料的选择更是重中之重。普通的金属在高温下会软化,塑料则会熔化,只有少数特殊材料能够在极端环境下保持稳定的物理特性。
这种高温压力传感器封装结构采用了多种先进材料。外壳部分使用了钽合金,这种材料不仅耐高温,而且具有良好的抗腐蚀性能。内部的关键部件则采用了碳化硅基材料,这种材料在高温下依然能够保持极高的硬度和稳定性。此外,为了防止热膨胀对传感器精度的影响,工程师们还特别设计了一种特殊的陶瓷填充层,有效缓解了温度变化带来的应力。
这些材料的组合使用,使得整个传感器能够在600摄氏度的高温下连续工作,同时承受高达1000个标准大气压的压力,远远超过了传统传感器的极限。
创新的封装工艺
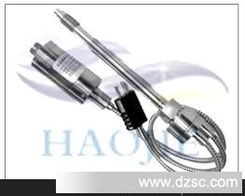
仅仅有好的材料还不够,如何将这些材料有效地组合在一起,形成稳定的封装结构,同样是技术关键。这种高温压力传感器采用了独特的三明治式封装工艺。
首先,将碳化硅基传感元件放置在中间层,这个元件是整个传感器的核心,负责将压力变化转换为电信号。在传感元件的上下两面分别覆盖一层钽合金基板,这些基板不仅起到保护作用,还负责将信号导出到外部。最外层则是一层特殊的陶瓷保护层,这种陶瓷材料具有良好的热稳定性和绝缘性能。
在整个封装过程中,工程师们还采用了特殊的真空注胶技术。通过将传感器内部抽真空,然后注入特制的环氧树脂胶,可以有效防止高温高压环境中的气体侵入,同时还能增强各层材料之间的结合力。这种封装工艺不仅提高了传感器的密封性能,还大大延长了其使用寿命。
多角度的性能分析
让我们从不同角度来分析这种高温压力传感器的性能表现。
从精度角度来看,这种传感器在500至600摄氏度的温度范围内,压力测量的误差可以控制在±0.5%以内。这个精度水平对于工业控制来说已经相当理想,能够满足大多数高温高压环境下的测量需求。更令人惊讶的是,即使在极端温度下,传感器的线性度依然保持得非常良好,没有出现明显的漂移现象。
在耐压性能方面,这种传感器经过严格的测试,证明其能够承受高达1500个标准大气压的压力冲击。在模拟的极端工业环境中,即使受到剧烈的压力波动,传感器也能在数秒内迅速恢复稳定测量,展现出出色的动态响应能力。
可靠性与耐久性也是衡量传感器性能的重要指标。经过1000小时的连续高温高压测试,这种传感器的失效率低于0.1%,远高于行业平均水平。一些使用该技术的石油钻探企业反馈,采用这种传感器后,钻探作业的故障率下降了30%,大大提高了生产效率。
应用场景与前景展望
这种高温压力传感器封装结构的应用前景非常广阔。在石油化工行业,它可以在炼油厂的高温高压反应釜中实时监测压力变化,为工艺优化提供准确数据。在能源领域,它可以用于燃气轮机的高温燃烧室,帮助工程师监控燃烧效率。在航空航天领域,这种传感器甚至可以用于火箭发动机的推力测量,为飞行安全提供保障。
随着工业4.0和智能制造的推进,对高温压力传感器的需求只会越来越多。未来,这种封装结构可能会进一步融合微机电系统(MEMS)技术,实现更小尺寸、更高集成度的传感器设计。同时,新材料的应用也可能进一步提升其性能指标,比如采用石墨烯基材料来提高传感器的灵敏度和响应速度。
一些行业专家预测,未来三年内,这种高温压力传感器将在更多极端工业场景中得到应用,特别是在新能源、深海探测和太空探索等领域。随着技术的成熟和成本的下降,它有望成为高温压力测量的新标准。
从材料选择到封装工艺